Corrosion Investigation
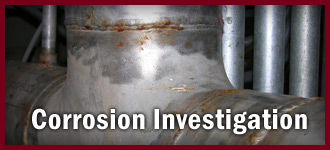
There are more than eight (8) types of corrosion.
General
General is the uniform and low level attack against the entire metal surface with little or no localized penetration. It is the least damaging of all forms of corrosion. Generalized, or uniform, corrosion usually occurs in environments in which the corrosion rate is inherently low or well controlled.
Galvanic
Galvanic is an aggressive and localized form of corrosion between two or more dissimilar metals in an electrically conductive environment. It occurs because the anodic material is attacked by the cathodic material.
Stress Corrosion Cracking
Stress Corrosion Cracking (SCC) is the cracking develops from the combination of tensile stress and a corrosive environment on a susceptible material. The required tensile stresses may be in the form of directly applied stresses or in the form of residual stresses
Crevice
Crevice is a localized form of corrosion usually associated with a stagnant solution on the micro-environmental level. Such stagnant microenvironments tend to occur in crevices (shielded areas) such as those formed under gaskets, washers, fastener heads, surface deposits, and clamps.
Pitting
Pitting can be present over the entire metal surface, creating an irregular or very rough surface profile. In other instances, pits are concentrated in specific areas, leaving the majority of the metal surface in like new condition. Pitting is accelerated, localized corrosion that can result in leaks without measurable metal loss of the entire component.
Microbiological
Microbiological a.k.a., MIC produces large and deep pits due to the microorganism's production of strongly corrosive metabolic by-products such as sulfuric acid that is capable of corroding metal.
Erosion
Erosion is the gradual and selective deterioration of a metal surface due to mechanical wear and abrasion. It is usually caused by entrained air bubbles, and / or high velocity particulates.
Dealloying
Dealloying a.k.a., selective leaching, refers to the selective removal of one element from an alloy by corrosion processes. A common example is the dezincification of unstabilized brass, which results in a weakened, porous copper structure.
An understanding of component configuration and environment and prior processing is important. Corrosion by-products are analyzed via SEM / EDS to characterize the chemical reactions that are necessary to produce the corrosion film.
Click here for more Product Details from
Reitz Consulting, Ltd...